Could soaring materials costs scupper the viability of housing projects?
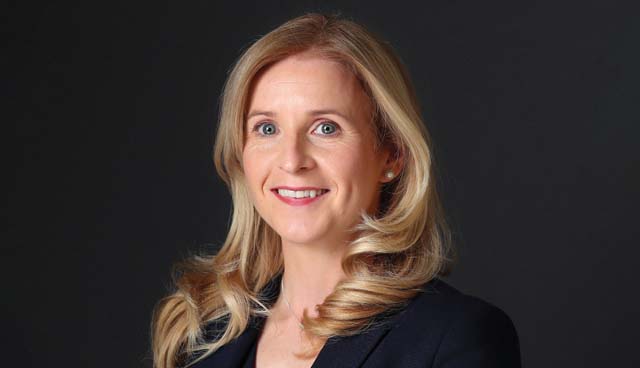
The construction industry returned to a very different landscape following its re-opening in May this year after the Covid-19-related lockdowns. As well as changes to on-site work practices, the Covid-19 pandemic has led to worldwide supply shortages resulting in an increase of as much as 30 per cent in the cost of some raw materials, writes Angelyn Rowan, partner in the construction, projects and PPP team at leading commercial law firm Philip Lee.
Add Brexit supply-chain issues to the equation and you have an industry facing significant challenges and inevitable cost increases affecting the viability of residential schemes as margins become even tighter. It is anticipated that the impact of some of these issues will begin to dissipate in 2022, but only time will tell. In the meantime, materials costs fluctuations and supply shortages continue to affect on-going projects, causing delays and driving cost increases, and will undoubtedly be a key consideration in future projects.
Current supply shortages
The construction industry is currently facing a supply crisis causing the costs of widely used materials, such as plastic and resins, to soar since early 2020. Building restrictions and increased disposable income during the Covid-19 lockdowns have resulted in strong product demand. Other factors, such as Brexit, are affecting transport and logistics, exacerbating supply issues.
Timber is also in great demand, with Covid-19, a licencing backlog slowing the felling of Irish trees and Brexit stockpiling all spelling trouble for an already pressurised market. The Irish Timber Frame Manufacturers’ Association first reported an unprecedented increase in timber prices in 2020, with the trend continuing in 2021. The Irish Home Builders Association is reporting that the cost of plywood has increased by up to 11 per cent since the start of 2021. They have reported that demand for sheet material in the US has caused a shortage worldwide.
Members of the Construction Ireland Federation (CIF) are reporting price increases of between 10 per cent and 30 per cent for steel, though the major issue appears to be sourcing sufficient supplies.
Approximately 60 per cent of the world’s aluminium originates in China. However, in recent years China has shut down many aluminium production facilities in an effort to reduce CO2 emissions, thereby greatly reducing production output. As a result, China is importing more aluminium from Europe, intensifying supply shortages and price increases. This has resulted in many Irish and foreign manufacturers reportedly having to close or limit their order books, blaming the ongoing shortages of raw materials and the exceptional demand.
Contractual approach to risk allocation for material costs fluctuations
Standard form construction contracts commonly contain clauses allowing for an adjustment to the ‘contract price’ to reflect any changes in the cost of materials (and labour) during the contract period. These clauses seek to compensate contractors for increases to their costs, which are caused by matters beyond their control. The traditional approach usually involves determining the increase in cost of materials using a base cost from published materials or a basic list of market prices included in the contractor’s tender. The duration of the project is a significant factor in the risk allocation between the employer and the contractor, with the employer being less likely to agree to a risk sharing approach on projects of a shorter duration or in the first few years of a project, where a contractor is arguably best placed to manage the risk. Contractors have called into question this approach in light of the recent price hikes, where the unprecedented events of the last 18 months have placed considerable risk and financial burden on contractors, potentially affecting the sustainability of a project.
The RIAI Building Contract makes provision for increased material and labour costs, with its Clause 36 allowing for an increase to the contract sum if these costs arise after the contract’s designated date. However, this provision is almost always amended, so that it is the contractor that bears the risk of any increases to material and labour costs throughout the duration of a project.
Under the Public Works Contract, where typically the PV1 clause is adopted, a contractor accepts the risk of increases to materials/labour costs. However, in the event of hyperinflation increases or where the increases have occurred outside the time period specified by the contract (i.e., beyond the 30-month limit) or the increases have occurred due to changes in law, the contractor has the potential to claim some portion of the costs.
We set out below a comparison table of the risk allocation for materials costs increases under the forms of construction contracts that are commonly used in Ireland.
Are extensions of time available where materials supply is delayed?
In terms of extensions of time, the default provisions in the RIAI Building Contract (Clause 30) allow for a contractor to seek an extension of time where it has been unable, for reasons beyond its control, to secure labour or materials that are essential for the proper execution of the works. This clause is commonly deleted, however, as an employer’s position is often that the contractor is best placed to manage this risk.
Delays brought about by the materials supply issues do not constitute grounds for a delay event under the Public Works Contract.
The JCT Contract (2016 Edition) makes no provision for an extension of time on the grounds that a contractor cannot secure materials.
Conclusion
The reality of supply shortages and escalating costs highlights the importance of contractors and employers knowing their contractual entitlements and considering the appropriate risk allocation in future projects. It may be the case that the parties to a contract will seek to negotiate bespoke provisions to re-balance what they may perceive as an unfair risk allocation.
Employers may seek to future-proof new projects and mitigate these risks by insisting that their design team members take account of materials availability risk when designing works and specifying products.
Given the events of the past 12-18 months and the extent of the increased material costs being faced by those in the industry, one can expect that these matters will continue to feature in contract claims in the foreseeable future and discussions involving the negotiation of construction contracts over the coming years.
Prepared with the assistance of Michael Cahill, Senior Associate at Philip Lee
For more information in relation to this article please contact Angelyn Rowan
T: +353 (0)1 237 3700
E: arowan@philiplee.ie
W: www.philiplee.ie